Peter Henderson
19/06/2024
Safety Integrity Level (SIL) is a crucial concept in industrial safety, especially in high-risk sectors like chemical processing, oil and gas, nuclear power, and transportation. It quantifies the level of risk reduction provided by safety functions, guiding the design and implementation of systems to ensure acceptable safety levels. SIL is governed by international standards such as IEC 61508 and IEC 61511, which focus on the functional safety of electrical, electronic, and programmable electronic systems.
The Concept of Safety Integrity Level
SIL represents a discrete level for specifying the safety integrity requirements of safety functions allocated to Electrical/Electronic/Programmable Electronic (E/E/PE) systems. The levels range from SIL 1 to SIL 4, with SIL 4 indicating the highest level of safety integrity and SIL 1 the lowest. Determining a SIL involves assessing the probability of failure on demand (PFD) and the frequency of operation, crucial for understanding potential system failures and their impacts.
Key Components of SIL
- Probability of Failure on Demand (PFD): PFD measures the likelihood that a safety system
will fail to perform its required function when needed. Each SIL corresponds to a specific PFD range, with lower values indicating higher reliability. - Risk Reduction Factor (RRF): RRF is the inverse of PFD, representing the risk reduction due to the safety function. For instance, a system with a PFD of 0.01 (SIL 2) has an RRF of 100, meaning it reduces the risk by a factor of 100.
- Safety Lifecycle: The safety lifecycle includes phases such as hazard and risk assessment, system design and implementation, operation and maintenance, and decommissioning, ensuring comprehensive safety management from conception to decommissioning.
- Functional Safety Standards: Standards like IEC 61508 and IEC 61511 provide guidelines for achieving SIL compliance, covering safety requirements specification, design, validation, and maintenance.
Adopting best practices relating to SIL will involve management of actions - whether from HAZOPS, risk assessments, reviews etc. These actions need to be carefully managed to ensure that they are completed within required timescales and that bottlenecks are clearly visible.
Using appropriate software can help to keep control of safety-critical actions and improve overall visibility of the processes involved in reducing risk.
Understanding Safety Functions
A safety function is a specific action or set of actions performed by a system to prevent or mitigate hazardous events. These functions are crucial for maintaining safety in industrial processes and can be broadly categorised into several types:
- Emergency Shutdown Systems (ESD): Designed to safely shut down a process or operation in case of an emergency, preventing accidents or minimizing their impact. For example, an ESD might automatically shut down a chemical reactor if it detects excessive pressure or temperature.
- Fire and Gas Systems (FGS): Detect fires or gas leaks and initiate appropriate actions such as activating alarms, shutting down equipment, or triggering fire suppression systems. These systems are vital in industries where flammable materials are handled.
- Safety Instrumented Systems (SIS): A broader category that includes systems designed to monitor process variables and take corrective actions to maintain safe operating conditions. SIS can include pressure relief systems, temperature control systems, and other automated safety measures.
- Pressure Relief Systems: These systems protect equipment and personnel by relieving excess pressure in vessels or pipelines. They often include pressure relief valves, rupture disks, and vent systems.
- Control Systems: Implement control loops to maintain process variables within safe limits. For example, a temperature control system might adjust the flow of coolant to prevent overheating in a reactor.
Determining SIL Requirements
The process involves several steps:
- Hazard Identification and Risk Assessment: Identifying potential hazards and assessing risks using techniques like Hazard and Operability Study (HAZOP) and Failure Modes and Effects Analysis (FMEA).
- Risk Analysis: Quantifying risks in terms of frequency and severity to understand hazard impacts and the need for risk reduction.
- Risk Reduction Measures: Identifying appropriate measures, including non-technical solutions (e.g., administrative controls) and technical solutions (e.g., safety instrumented systems).
- SIL Determination: Using methods like risk graphs and Layers of Protection Analysis (LOPA) to assign SIL levels to safety functions based on required risk reduction (Fig 1).
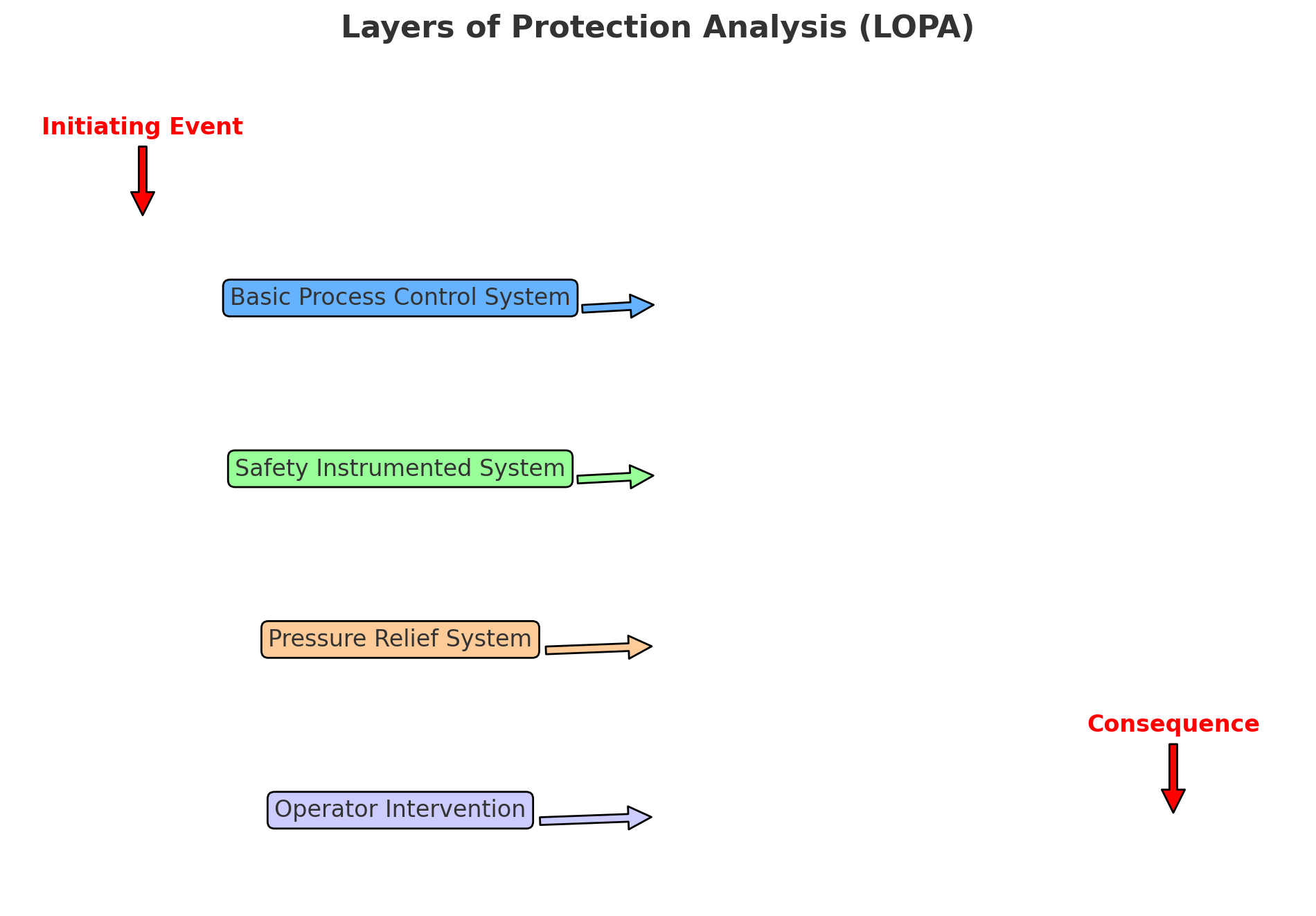
Figure 1 - LOPA - Layers of protection
SIL Levels and Their Implications
Each SIL level has specific implications:
- SIL 1: PFD 0.1 to 0.01. Provides basic risk reduction, requiring less stringent design and testing.
- SIL 2: PFD 0.01 to 0.001. Requires moderate risk reduction, with more rigorous design and testing.
- SIL 3: PFD 0.001 to 0.0001. Provides high risk reduction, necessitating stringent design, testing, and maintenance.
- SIL 4: PFD 0.0001 to 0.00001. Represents the highest risk reduction, requiring the most rigorous processes.
Practical Application of SIL
Implementing SIL involves:
- Design and Engineering: Ensuring design compliance with the required SIL, selecting appropriate components, and designing fault-tolerant architectures.
- Validation and Verification: Rigorous testing under various conditions to ensure compliance with required SIL.
- Operation and Maintenance: Regular testing, inspection, and maintenance to ensure ongoing compliance.
- Documentation and Training: Comprehensive documentation and training to ensure proper operation and maintenance.
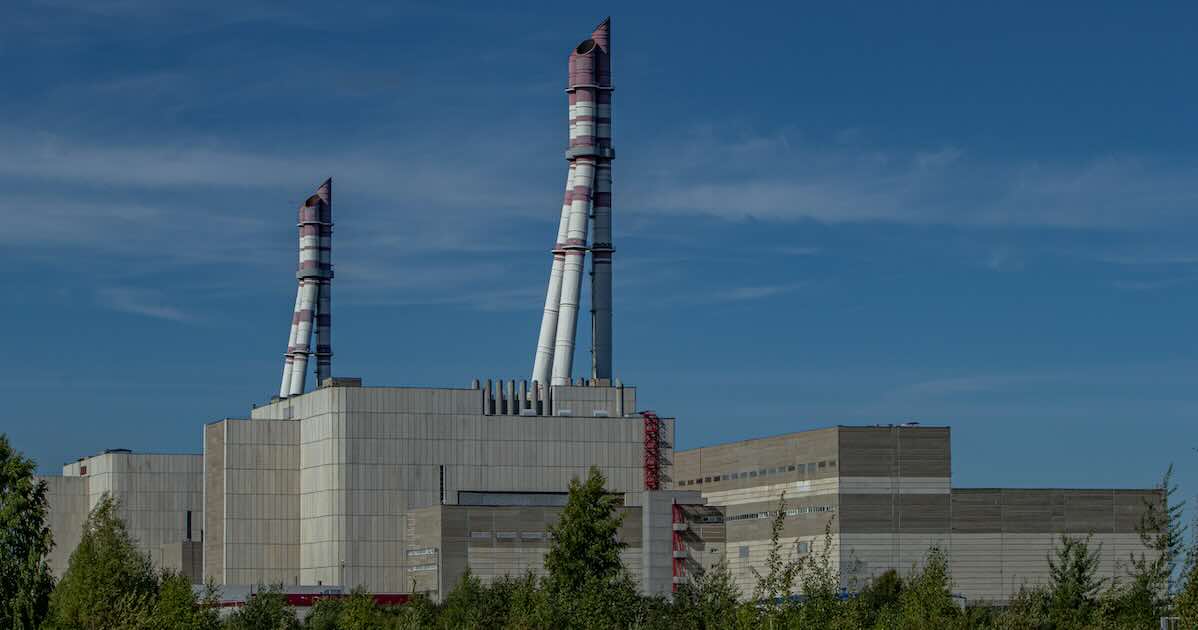
Case Study: SIL in the Process Industry
In the process industry, SIL is applied to safety instrumented systems (SIS) controlling critical processes, such as the shutdown of reactors in chemical plants during abnormal operating conditions.
A Safety Instrumented System is an engineered set of hardware and software controls used to achieve or maintain a safe state of a process when predetermined conditions are violated. SIS functions by detecting abnormal conditions and initiating pre-defined actions to prevent accidents. These actions can include shutting down equipment, venting gases, or activating alarms to alert operators to take corrective measures.
- Hazard Identification and Risk Assessment: A HAZOP study identifies potential hazards such as overpressure in a reactor. The risk assessment quantifies the potential impact and likelihood of an overpressure event.
- Risk Reduction Measures: The risk analysis might determine that existing control systems are insufficient, necessitating additional measures like an SIS.
- SIL Determination: Using methods like LOPA, the required SIL for the SIS is determined. Suppose the analysis indicates that the risk reduction needed corresponds to SIL 3. This means the SIS must achieve a PFD between 0.001 and 0.0001.
- Design and Engineering: The SIS is designed to meet SIL 3 requirements, involving the selection of reliable components and the implementation of fault-tolerant architectures.
- Validation and Verification: The SIS undergoes extensive testing to ensure it meets SIL 3 standards, including functional and scenario-based testing.
- Operation and Maintenance: A maintenance schedule is implemented to include regular testing and inspection of the SIS to ensure it continues to meet SIL 3 requirements.
- Documentation and Training: Detailed documentation of the SIS design, testing, and maintenance procedures is maintained, and personnel are trained in the operation and maintenance of the SIS.
Challenges and SIL Best Practices
Implementing and maintaining SIL-compliant systems comes with challenges:
- Complexity: Higher SIL levels require more complex designs and rigorous testing, making management challenging.
- Cost: Achieving higher SIL levels involves significant costs for design, testing, and maintenance, necessitating a balance between safety and cost.
- Regulatory Compliance: Ensuring compliance with standards like IEC 61508 and IEC 61511 requires ongoing effort.
- Human Factors: Human error can impact the effectiveness of safety systems, emphasising the need for comprehensive training and clear procedures.
Best Practices Include
- Early Involvement: Involving safety engineers early ensures safety requirements are integrated into the design from the beginning.
- Regular Reviews: Conducting regular safety reviews and audits helps identify potential issues and ensures ongoing compliance with SIL requirements.
- Continuous Improvement: Implementing a culture of continuous improvement helps organisations adapt to changing safety requirements and technological advancements.
- Stakeholder Engagement: Engaging all stakeholders ensures a comprehensive understanding of safety requirements and fosters a culture of safety.
Action Tracking Software
The Pisys Action Tracker is Action Tracking Management Software (ATMS) used by thousands of safety professionals worldwide to ensure that high-governance actions are appropriately managed. Read how Wood plc use Action Tracker for its effectiveness in ensuring safety, and improving oversight across global operations.