Peter Henderson
In risk management and safety engineering, Failure Modes and Effects Analysis (FMEA) and Hazard Analysis (HA) are widely used methodologies. Both aim to identify potential failures and hazards within systems, processes, or designs, but they differ significantly in their approaches, applications, and outcomes. We'll look at the key differences between FMEA and Hazard Analysis, exploring their methodologies, applications, advantages, and limitations.
What is FMEA?
FMEA (Failure Modes and Effects Analysis) is a systematic method for evaluating processes to identify where and how they might fail and assessing the relative impact of different failures. It is primarily used to improve the quality, reliability, and safety of products or processes. FMEA can be applied during the design phase (Design FMEA) or the process phase (Process FMEA).
Key Elements of FMEA
- Failure Modes: Potential ways in which a process or product could fail.
- Effects Analysis: The consequences of these failures on system operations, end-users, or product quality.
- Severity, Occurrence, and Detection: These factors are rated to calculate a Risk Priority Number (RPN) which prioritises issues that need addressing.
- Mitigation Actions: Steps to reduce or eliminate the potential failures identified.
What is Hazard Analysis?
Hazard Analysis (HA) is a broad methodology that encompasses various techniques used to identify potential hazards in systems, processes, or products. Unlike FMEA, which is a specific type of analysis, Hazard Analysis includes several methods such as Preliminary Hazard Analysis (PHA), Fault Tree Analysis (FTA), Event Tree Analysis (ETA), and more. The main goal of Hazard Analysis is to systematically identify and evaluate hazards to prevent accidents and ensure safety.
Key Elements of Hazard Analysis
- Hazard Identification: Recognizing potential sources of harm or danger.
- Risk Assessment: Evaluating the likelihood and severity of hazards.
- Risk Control: Implementing measures to mitigate or eliminate identified hazards.
- Documentation and Review: Keeping detailed records of hazards and control measures, and reviewing them regularly.
Methodological Differences Between FMEA & Hazard Analysis
The fundamental difference between FMEA and Hazard Analysis lies in their scope and methodological approaches.
FMEA Methodology
FMEA is a bottom-up approach that focuses on individual components or steps in a process. It starts with identifying all possible failure modes for each component, analysing the effects of these failures, and then prioritising them based on severity, occurrence, and detection. This approach is more quantitative, as it involves calculating RPNs to prioritise risks.
Steps in FMEA

- Identification: List all components or steps.
- Analysis: Identify potential failure modes for each component.
- Assessment: Evaluate the effects of each failure mode and rate them based on severity, occurrence, and detection.
- Prioritisation: Calculate RPNs and prioritise failure modes that need attention.
- Action: Develop and implement actions to mitigate high-priority risks.
Hazard Analysis Methodology
Hazard Analysis is a more flexible and comprehensive approach that can be tailored to different contexts and requirements. It can be top-down, bottom-up, or a combination of both, depending on the specific technique used. Here are brief descriptions of some common Hazard Analysis techniques:
- Preliminary Hazard Analysis (PHA): A qualitative approach used early in the design phase to identify potential hazards and assess their severity.
- Fault Tree Analysis (FTA): A top-down method that uses a tree-like diagram to analyse the pathways that can lead to a specific undesirable event.
- Event Tree Analysis (ETA): A forward-looking approach that starts from an initiating event and examines possible outcomes using a tree structure.
- Hazard and Operability Study (HAZOP): A detailed, systematic examination of process deviations and their consequences.

Steps in Hazard Analysis
- Preparation: Define the scope, select the appropriate technique, and gather relevant data.
- Hazard Identification: Systematically identify potential hazards using the chosen technique.
- Risk Assessment: Evaluate the likelihood and severity of identified hazards.
- Risk Control: Develop and implement measures to mitigate or eliminate hazards.
- Documentation and Review: Record findings and control measures, and review them periodically.
The Role of Action Tracking
Both approaches will inevitably require actions to be taken to either prevent failure or mitigate hazards. The Pisys Action Tracker has been used for FMEA, HAZOP and HAZID studies worldwide since 2001 and is the tool of choice for process safety professionals.
Applications and Industry Use
The choice between FMEA and Hazard Analysis often depends on the industry and specific application.
FMEA Applications
FMEA is versatile and can be applied across various industries, including automotive, aerospace, electronics, and manufacturing. It is particularly useful in:
- Design Phase: Identifying potential design flaws and improving product reliability.
- Process Improvement: Enhancing manufacturing processes by identifying and mitigating potential failures.
- Maintenance: Developing preventive maintenance plans based on failure mode analysis.
For example, in the automotive industry, FMEA might be used to analyse potential failures in a new braking system design. The analysis would identify failure modes such as brake fluid leakage, assess the severity of each failure mode (e.g., reduced braking efficiency or total brake failure), and prioritise actions to mitigate these risks, such as improving seal designs or using higher-quality materials.
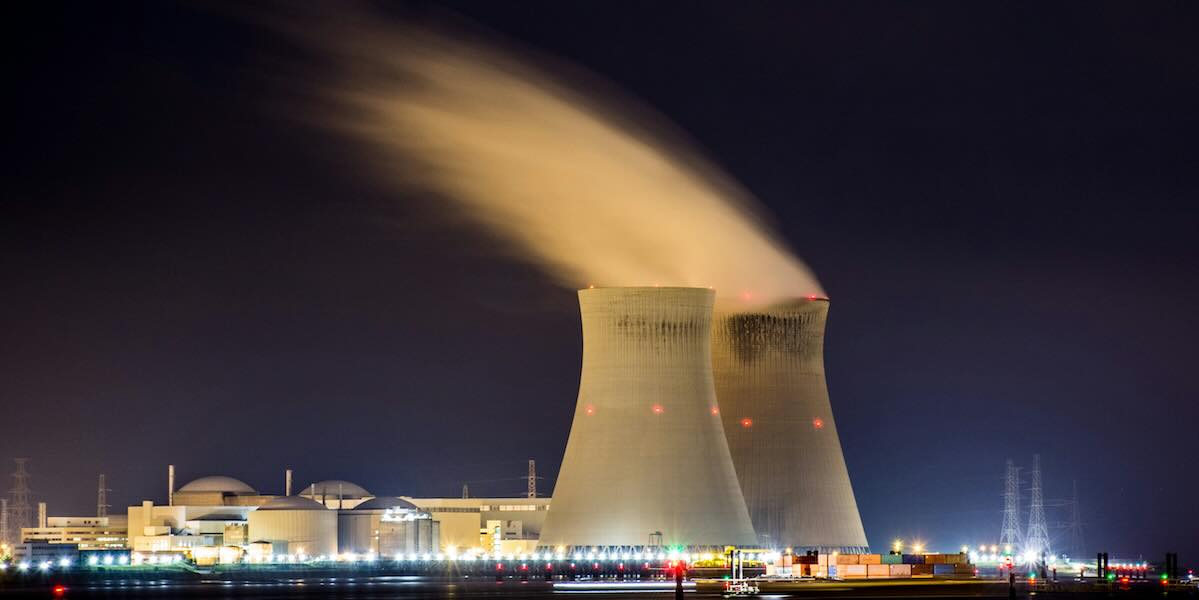
Hazard Analysis Applications
Hazard Analysis is predominantly used in industries where safety is paramount, such as:
- Chemical Processing: Identifying and mitigating risks in chemical plants.
- Pharmaceutical Manufacturing: Ensuring safety and compliance in drug production processes.
- Oil and Gas: Enhancing safety and operability in oil refineries and offshore platforms.
- Aerospace: Ensuring the safety of aircraft design and operation.
- Nuclear Power: Identifying and mitigating potential risks in nuclear power plants.
For instance, in a chemical plant, Preliminary Hazard Analysis (PHA) might be used during the design phase to identify potential chemical spill hazards. Fault Tree Analysis (FTA) could be applied to analyze the causes of a potential reactor explosion, while Event Tree Analysis (ETA) might be used to examine the possible outcomes of a valve failure. Each technique provides a different perspective on hazards and helps to develop a comprehensive risk management strategy.
Advantages and Limitations
Both FMEA and Hazard Analysis have their unique advantages and limitations.
FMEA Advantages
- Quantitative Analysis: Provides a numerical basis for prioritising risks.
- Broad Applicability: Can be used in various phases and industries.
- Preventive Approach: Focuses on preventing failures before they occur.
FMEA Limitations
- Resource Intensive: Can be time-consuming and requires detailed knowledge of the system.
- Component Focus: May overlook system-level interactions and holistic process issues.
Hazard Analysis Advantages
- Comprehensive Approach: Can be tailored to different contexts and needs.
- Versatility: Includes various techniques for different types of hazards.
- System-Level Perspective: Considers both component-level and system-level hazards.
Hazard Analysis Limitations
- Complexity: Can be complex and require significant expertise to conduct effectively.
- Qualitative Nature: Some techniques rely on qualitative assessments, which may be subjective.
- Resource Intensive: Can be time-consuming and require detailed data and multidisciplinary teams.
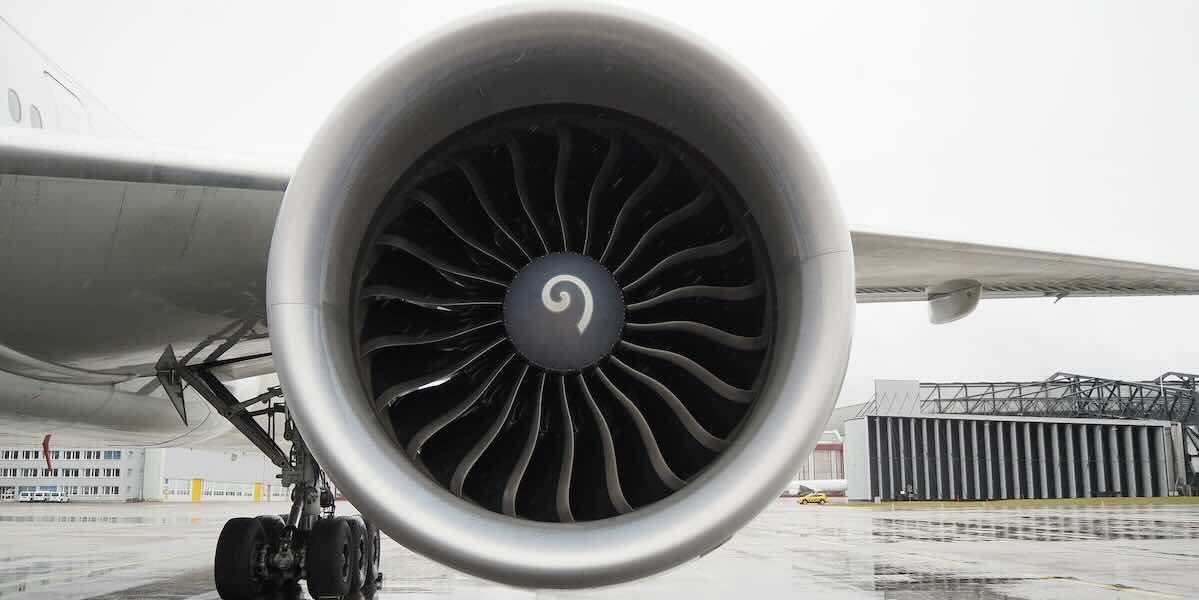
Choosing Between FMEA and Hazard Analysis
Selecting between FMEA and Hazard Analysis depends on the specific context and requirements of the project.
- Use FMEA When:
- A detailed, component-level analysis is needed.
- Quantitative prioritisation of risks is required.
- The focus is on product design, process improvement, or preventive maintenance.
- Use Hazard Analysis When:
- A comprehensive, system-level examination is necessary.
- The project involves complex processes with significant hazards.
- A flexible approach is needed to tailor the analysis to specific hazards.
Integrating FMEA and Hazard Analysis
In some cases, integrating both FMEA and Hazard Analysis can provide a more comprehensive risk analysis. For example, an organisation might use FMEA during the design phase of a new product to identify potential component failures and then apply Hazard Analysis during the operational phase to examine system-level hazards. This dual approach ensures that both product reliability and system safety are thoroughly addressed.
For instance, in the aerospace industry, FMEA might be used to analyse potential failures in a new aircraft engine design, identifying specific component failures like turbine blade fractures. Subsequently, Hazard Analysis techniques like Fault Tree Analysis (FTA) could be used to explore the broader consequences of an engine failure during flight, considering system-level interactions and potential cascading effects.
Conclusion
FMEA and Hazard Analysis are both vital tools in risk management and safety engineering. While FMEA offers a structured, quantitative approach to identifying and mitigating potential failures at the component level, Hazard Analysis provides a flexible, comprehensive examination of hazards at both the component and system levels. Understanding their differences, methodologies, applications, and limitations is crucial for selecting the appropriate tool to ensure safety, reliability, and efficiency in various industries. By leveraging the strengths of each methodology, organisations can better anticipate and mitigate risks, ultimately enhancing their overall operational safety and performance.
Whether choosing FMEA, Hazard Analysis, or a combination of both, the key is to systematically and thoroughly analyse potential risks, implement effective mitigation strategies, and foster a culture of continuous improvement and safety awareness.